Induction furnace repair and overhaul
Sephan Elgha Engineering Company has always strived to enhance the quality of its design, manufacturing, and after-sales services in a way that extends the lifespan of its products beyond what is typically expected in the industry. Currently, products from this company that have been overhauled on time and received proper maintenance have been upgraded in terms of control system technology, electronics, and capabilities and features related to technology that contribute to increased efficiency and productivity. Many features of the latest technological advancements have also been implemented in the company’s older products.
The company performs major repairs and overhauls of furnaces at its customers’ plants in the following areas:
Induction coil overhaul
Regular servicing of induction coils plays a crucial role in the lifespan and efficiency of furnaces. If the customer lacks the facilities for coil repair or service, the coil will be fully serviced at the Sephan Elgha company’s factory and returned to the customer.
Typically, in foundry and steelmaking industries, furnaces exceeding 2 tons require coil servicing after six months of continuous operation. For furnaces with a capacity less than 2 tons, coil servicing is typically needed every two years.
Coil service includes repairing or restoring damaged parts, descaling, surface cleaning, insulation, and conducting insulation and leakage tests.
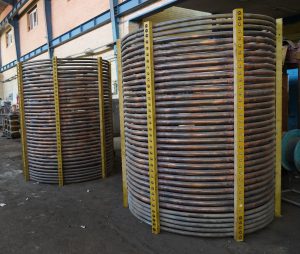
Frequency Converter Panel Service
All repairs on frequency converter panels are performed at the customer’s factory, but typically, panels require a complete overhaul after five years. Usually, within this timeframe, the control system technology of the furnaces is upgraded or the components used are updated. If the panels are overhauled on time, the technology of electronic circuits, consumable parts, and functions used will always be updated, and by compensating for furnace wear and tear, they will always be ready to operate at maximum efficiency.
A general overhaul of frequency converter panels includes the following:
- Descaling heat sinks and water collectors of the cooling circuit.
- Repair or replacement of cooling circuit valves.
- Replacement of all pneumatic connections and hoses in the cooling circuit.
- Cleaning areas where insulation is critical.
- Insulating areas with voltage relative to the body.
- Replacing electronic boards whose components are obsolete and cannot be sourced in the future.
- Cleaning and insulating electronic boards.
- Upgrading the control system software, including the control board, PLC, and the device monitoring system.
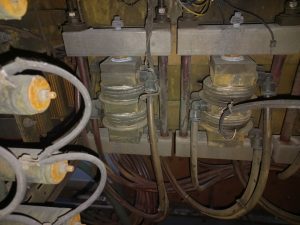
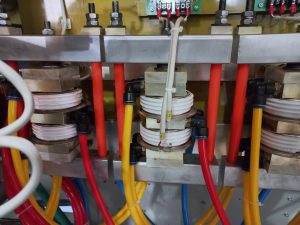
Main Transformer Service
The furnace transformer is a critical component of the furnace. Due to its high cost and manufacturing time, obtaining a replacement can pose significant challenges compared to other furnace components. This underscores the importance of timely and accurate transformer servicing.
Routine maintenance performed at the customer’s plant includes: continuously monitoring the transformer temperature, ensuring the cleanliness of the transformer body and insulators, securing input and output connections, preventing excessive load on insulators by cables, verifying the correct operation of the protective relays in the transformer power supply circuit, and ultimately ensuring the quality of the transformer oil.
It is recommended that a complete service and overhaul of the transformer be performed every two years. During a general overhaul, the transformer oil is also filtered or replaced if necessary.
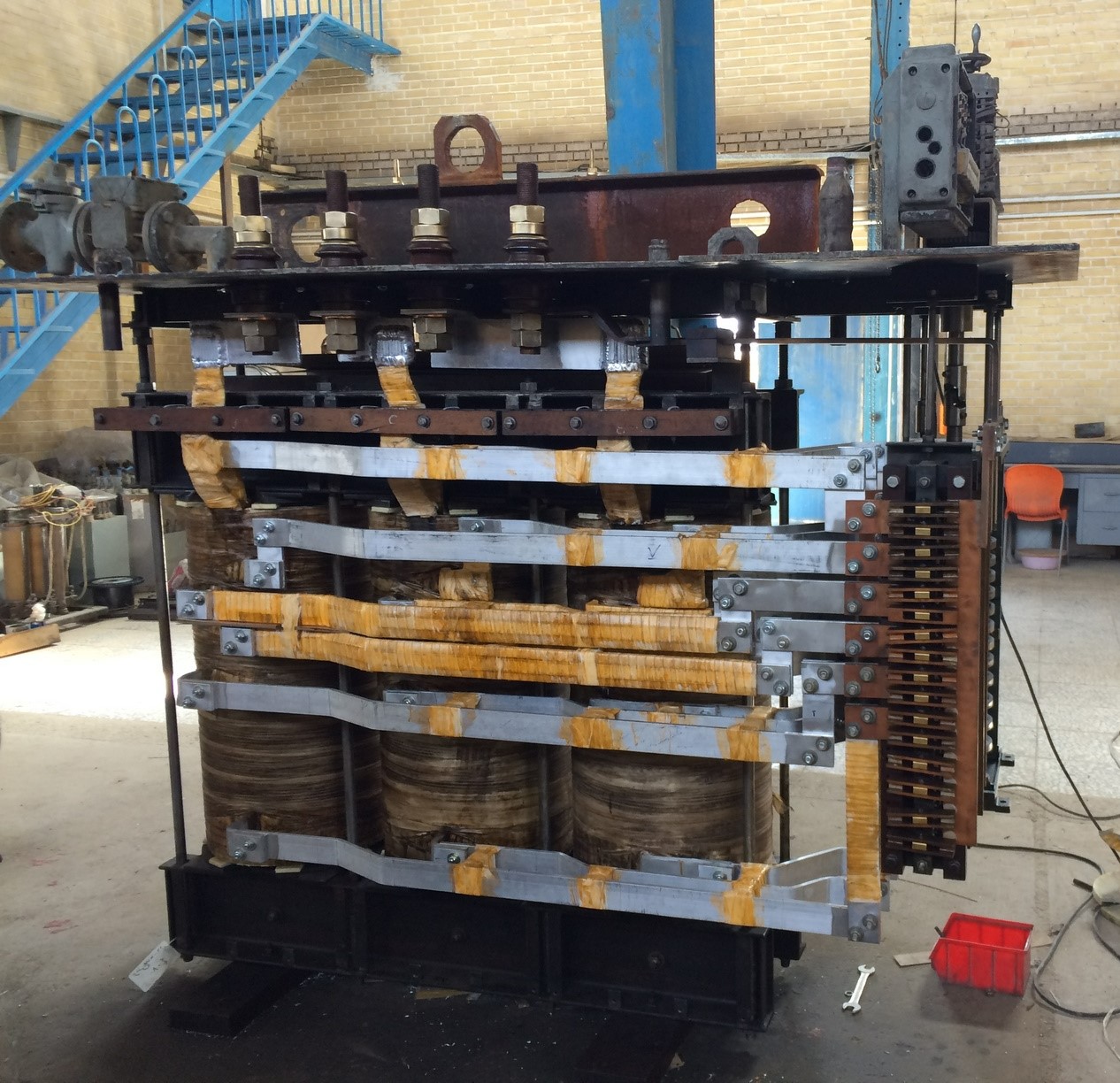
Reactor Service
From a maintenance perspective, the DC choke in induction furnaces is very important because repair or procurement can be time-consuming, and a failure or major overhaul can lead to a shutdown of at least a few days. Therefore, adhering to the following points is recommended to minimize the need for overhauls or emergency repairs:
- Use distilled water free of any minerals in the cooling circuit to prevent the formation of deposits and, consequently, a decrease in heat transfer within the cooling circuit.
- Use a filter in the cooling circuit to prevent any foreign materials from entering the choke and blocking the water circulation path.
- Prevent dust from settling on the choke, which can lead to electrical conductivity, resulting in crawling currents and ultimately arcing, causing damage to the choke coils.
- Perform timely tightening of bolts to prevent loosening of electrical or mechanical connections, which can lead to accidents and failures.
Major choke repairs at the Sephan Elgha factory include:
- Descaling the water paths of the cooling system.
- Thoroughly cleaning the coils and removing all metallic dust.
- Insulating the coils with a special insulating coating that is resistant to heat, moisture, and electrical conductivity.
- Cleaning, re-ordering, and if necessary, repairing the choke core.
- Replacing the insulation used in electrical and mechanical connections.
- Readjusting the necessary air gaps for proper choke operation.
- Conducting insulation, leakage, and functional tests.
Capacitor Bank Service
The capacitor bank in furnaces is one of the components that is overhauled at the customer’s factory, usually by the maintenance team stationed there. The following are typically recommended during periodic repairs:
- Cleaning insulators (weekly): This ensures proper insulation and prevents electrical faults.
- Replacing insulators if damaged (daily): Damaged insulators can compromise the system’s safety and efficiency.
- Replacing or repairing connections with water leaks (daily): Water leaks can cause short circuits and damage to the capacitor bank.
- Replacing all pneumatic connections and hoses in the cooling water circuit (maximum once every 5 years): This helps ensure proper cooling and prevent potential leaks.
- Tightening all electrical connections (monthly): Loose connections can cause overheating and potential hazards.
- Visual inspection and monitoring the temperature of the capacitor bodies (daily): This helps detect any signs of overheating or malfunction.
Furnace Selection Switch Service
The furnace selection switch is a type of offline break switch that is pneumatically operated, connecting the furnace to the capacitor bank. Due to its operation at several kilovolts and several kiloamperes, this switch is highly sensitive. Following these points will extend the switch’s lifespan and efficiency:
- Regular Cleaning of Blades: Keep the blades consistently clean.
- Clean and Dry Insulator Supports: Ensure the insulator supports are clean and dry.
- Prevent Water Spray and Leaking Connections: Prevent water from spraying onto the switch and address any leaks in the connections.
- Ensure Proper Adjustment of Moving Connections: Confirm the moving connections are properly adjusted.
- Do Not Manipulate Moving Connections: Experienced service personnel should be involved in adjusting connections. Training or supervision is mandatory.
- Compressed Air Pressure: Ensure a minimum of 6 bar compressed air pressure for complete switch opening and closing.
- Verify Switch Position Sensors: Ensure the switch position sensors are functioning correctly.
Important Note: If the switch is out of adjustment, resulting in overheating or arcing on the blades, the blades must be sent to Sephan Elgha factory for a comprehensive service, or replaced.
Cooling Tower Repair and Overhaul
Cooling towers are crucial components whose proper functioning directly impacts the efficiency, lifespan, and downtime reduction of the equipment.
Cooling towers are constantly exposed to damage and wear due to impurities in the water, making regular maintenance crucial. Descaling is one of the most important tasks performed during cooling tower servicing by the maintenance personnel stationed at the factory. Replacing the packings or other consumable parts in the cooling tower can also be done on-site by the customer’s maintenance personnel.